Assay Development
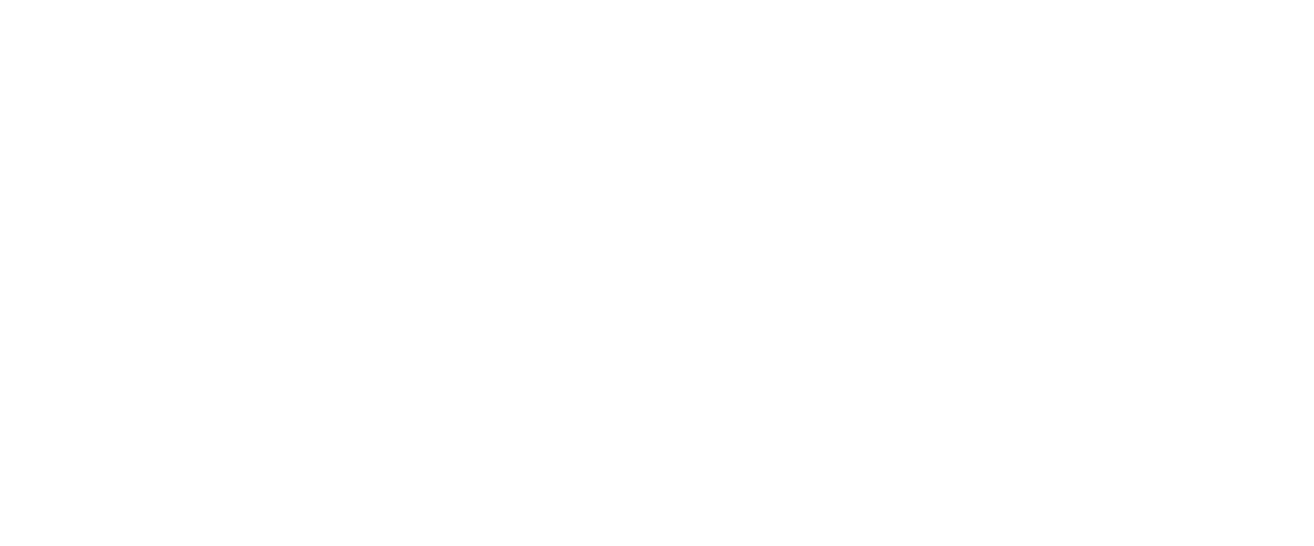

We at Palladium Diagnostics are experts in immunoassay development and will provide you with the ideal partner to assist you in the optimization and commercialization of your diagnostic products. From concept and design, initial feasibility, through the product development stage, Verification & Validation and all the way to commercial launch and manufacturing, Palladium Diagnostics is a trusted partner capable of delivering your product on-time and on-budget.
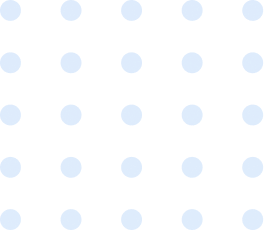
Decades of Success, and Hundreds of Assays Developed
Complete Turnkey Solutions
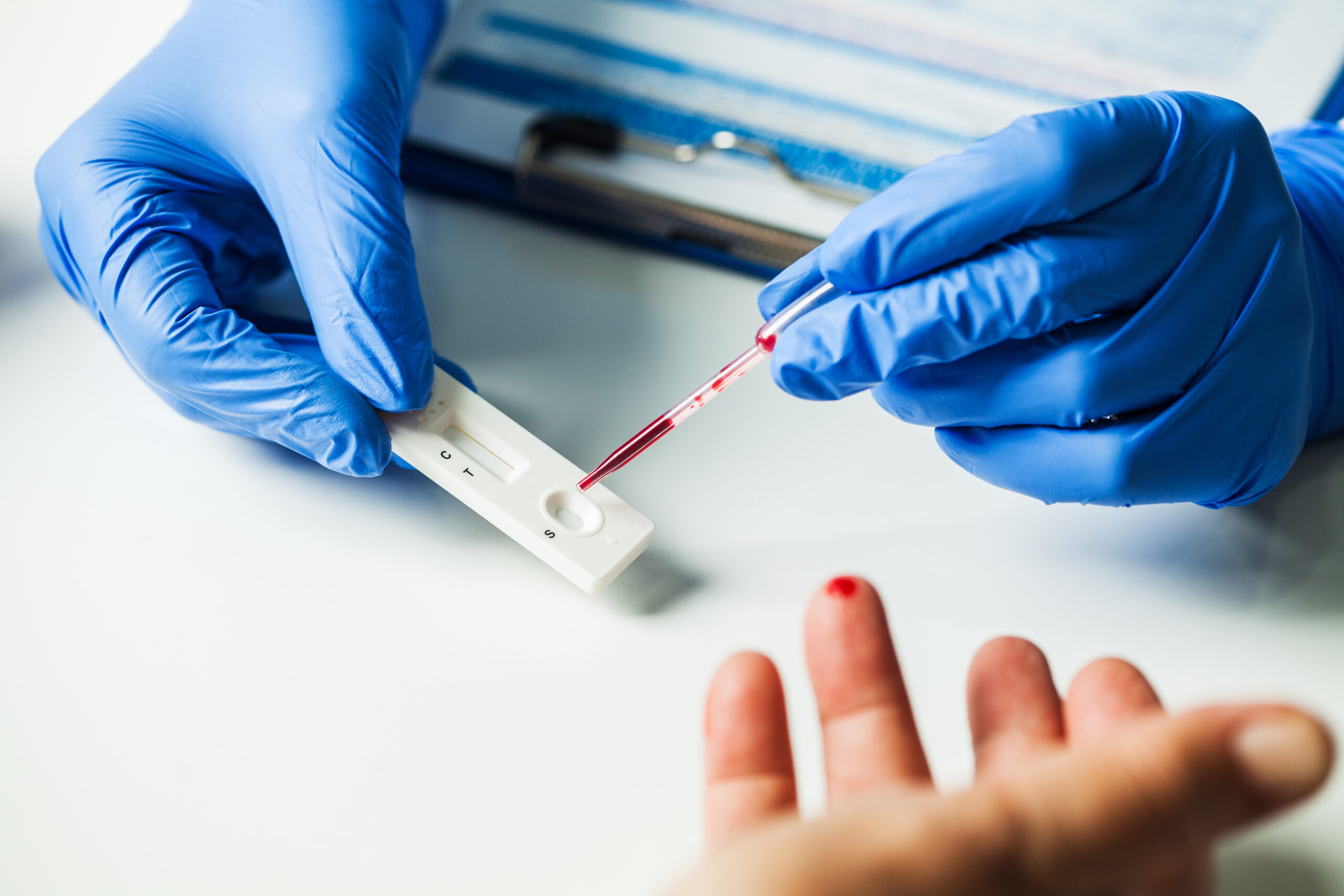
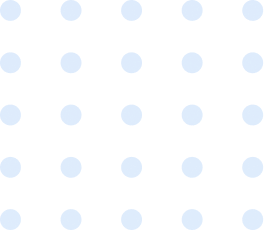
Assay Formats
Assay Formats
Sample Types
Assay Configerations
Labels
The Palladium Development Process
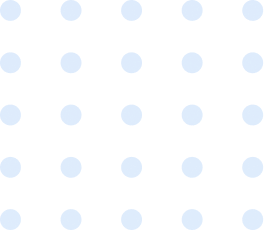
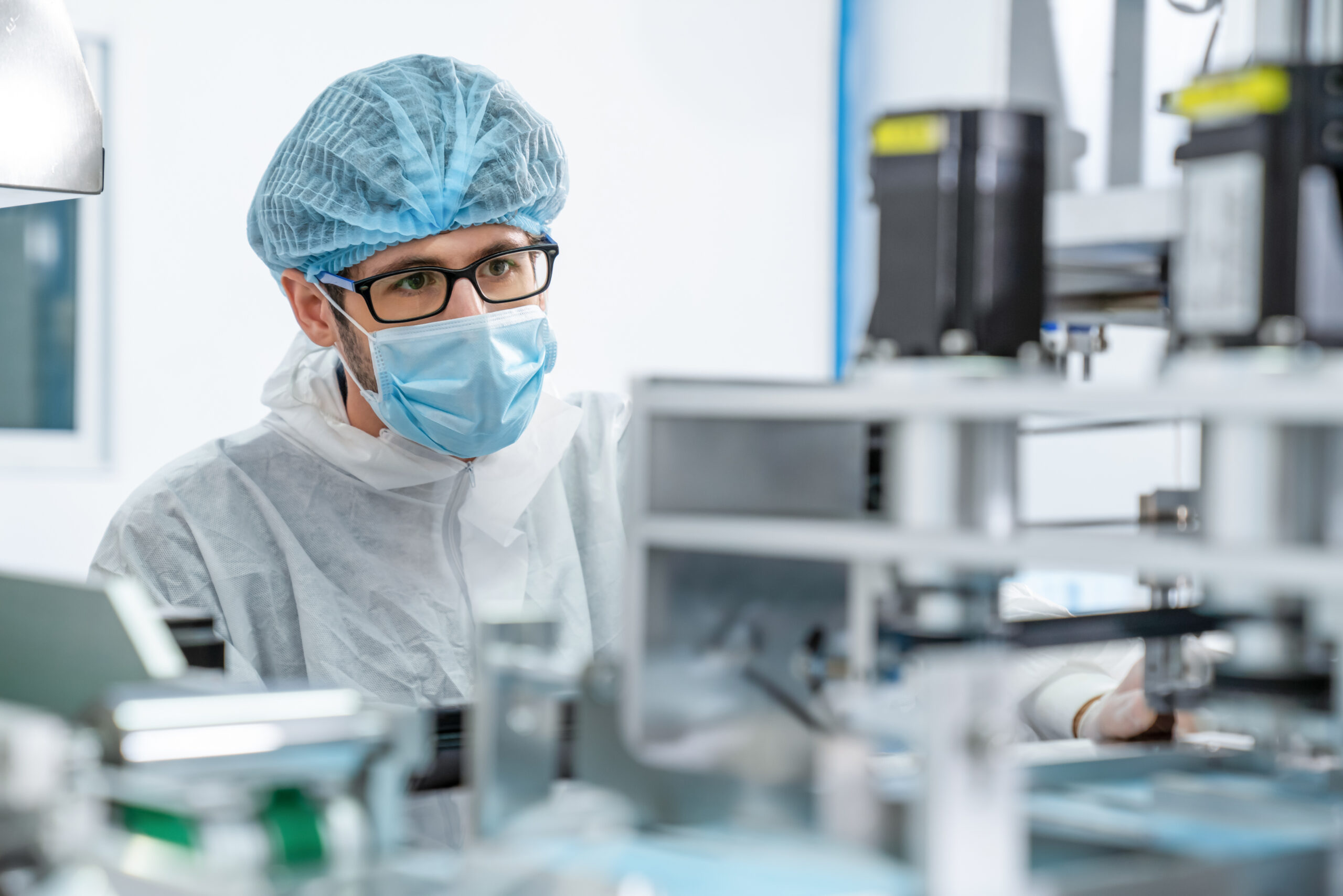
Phase 1
Feasibility and Prototyping is setting initial design criteria, reviewing market research, and reducing the technology to practice. Careful planning and management can decrease the timeline and costs of product development.
Specific tasks are:
Define product requirements.
Technology assessment.
Put together the R&D plan for the product prototype.
Source reagent & materials.
Develop the initial assay/prototype.
Conduct a phase review to focus the product development team.
Go or no-go decision!
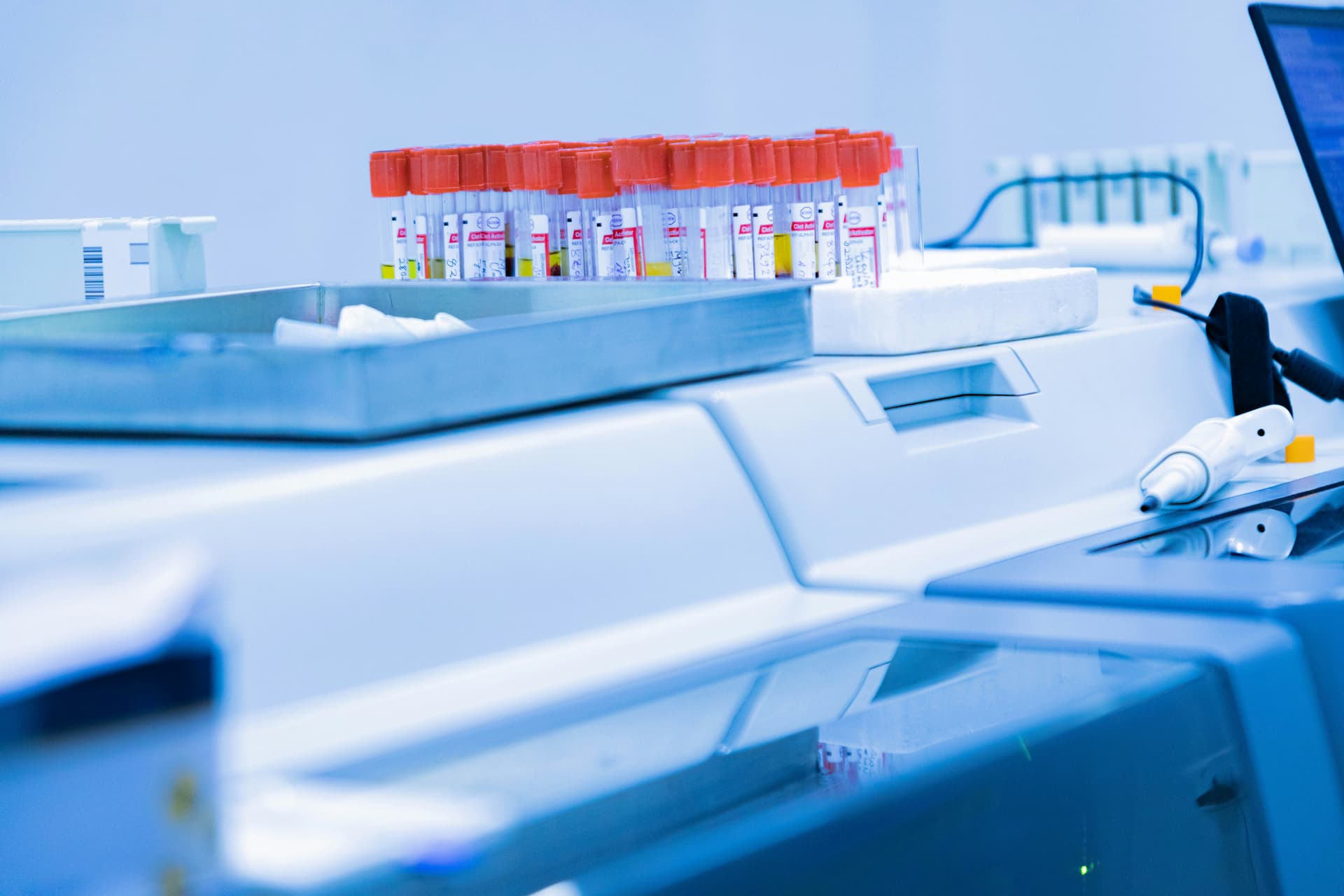
Phase 2
Product Design & Development moves from a primarily research phase into true development. This transition is critical as trade-offs are often necessary between R & D, Manufacturability, and Market needs.
Specific activities for Phase 2:
- Conduct a technical review of work to date.
- Define the timeline and costs for the project.
- Draft and execute the Design & Development plan.
- Finalize performance specifications.
- Bring together the product development, management, manufacturing, and marketing teams.
- Prepare the Device Master Record (DMR)
- Phase review.
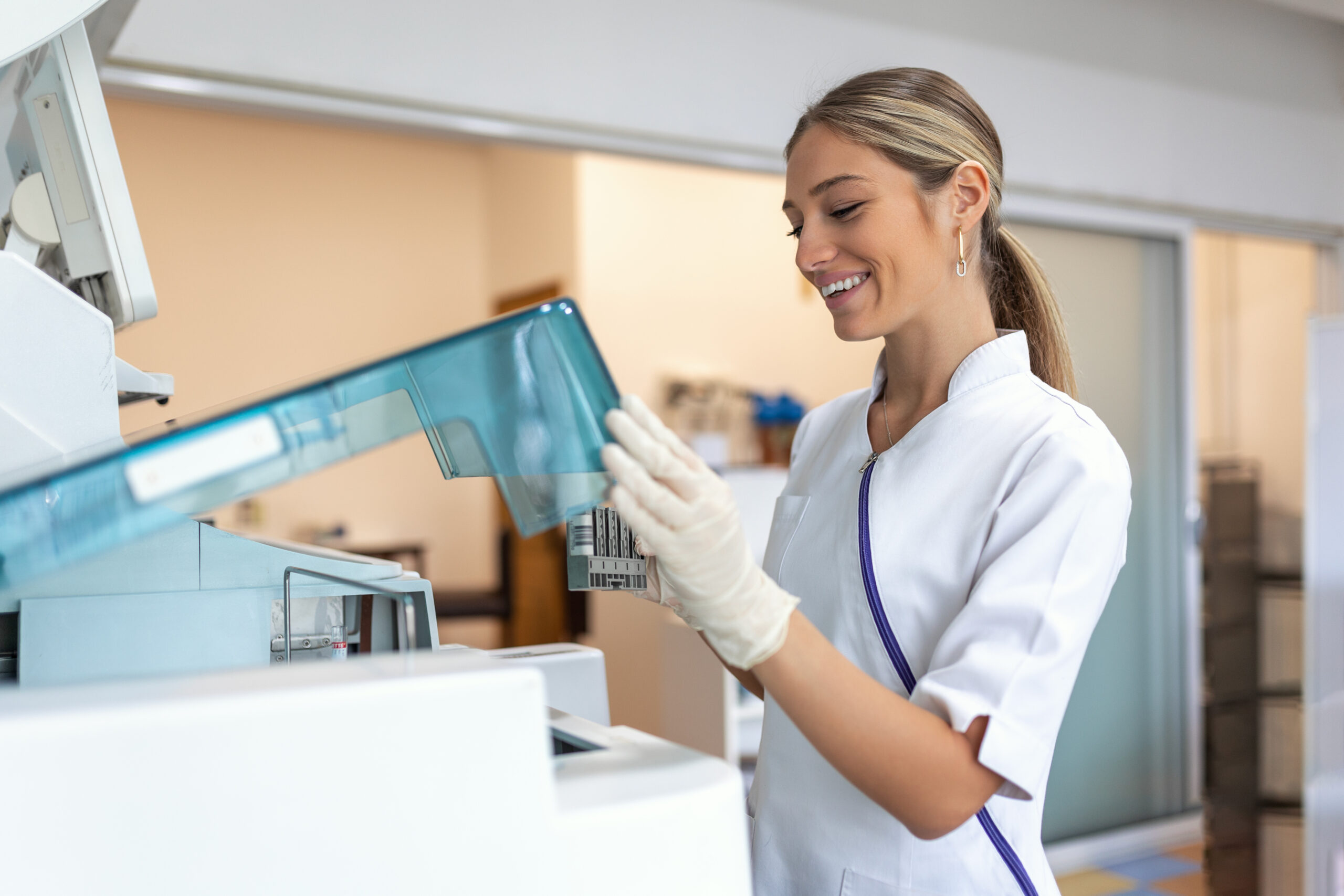
Phase 3
Manufacturing Transfer covers all tasks necessary to transition the product from R & D/Product Development to the Manufacturing team:
- Transfer all documentation to include SOPs, Batch Records, RMS, and QC documents with comprise the DMR.
- Install product at the Manufacturing site.
- Train Manufacturing & QC personnel.
- Prepare pilot batch and conduct thorough internal validation.
- Finalize packaging design.
- Complete final manufacturing & QC documents.
- Prepare for a site visit by regulators.
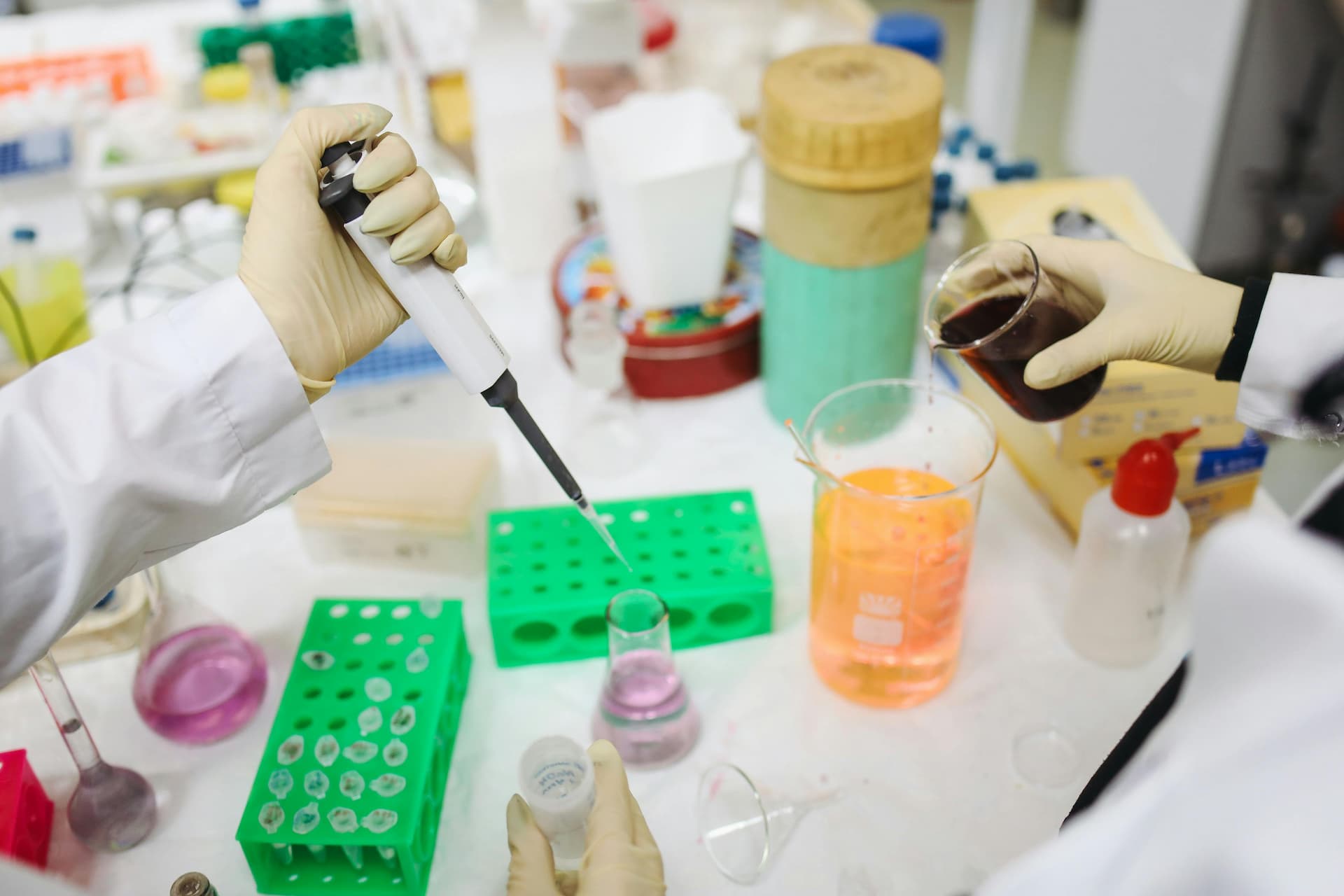
Phase 4
Design Verification. After development has been largely accomplished, the product must be verified to test its reproducibility and accuracy using assay components and reagents.
Steps in Phase 4 include:
- Prepare pilot lots of assay components and reagents.
- Build pre-production lots of complete assay.
- Finalize QA/QC methods.
- Draft Verification plan & Verification Studies.
- Draft Flex study plan and protocols.
- Execute all studies and prepare Verification Report.
- Create the initial marketing plan.
- Prepare for clinical trials as necessary.
Phase 4 will prove whether the assay can meet its design and performance specifications. In most cases, this phase will take more time and cost more than expected.

Phase 5
Product Validation. At this stage of development, the final product performance and format should be complete, thus ready for clinical trials. Clinical Trials commence once pilot product is built and verified, the clinical evaluation of the product begins.
Phase 5 tasks:
- Produce at least three pilot batches of all assay reagents and components to specifications.
- Review Design and Manufacturing considerations.
- Meet with the appropriate regulatory agencies for regulatory submissions (e.g., 510(k), or CE Mark).
- Prepare Clinical Trial plan.
- Train personnel at clinical trial sites.
- Shipping assay kits and/or reagents.
- Data collection and review.
- Provide troubleshooting and technical assistance as needed.
After the trials are complete, data must be interpreted & compiled. Documentation for regulatory submissions can be difficult; many companies contract a third-party CRO for clinicals and data handling/documentation. Palladium Dx can be your partner.
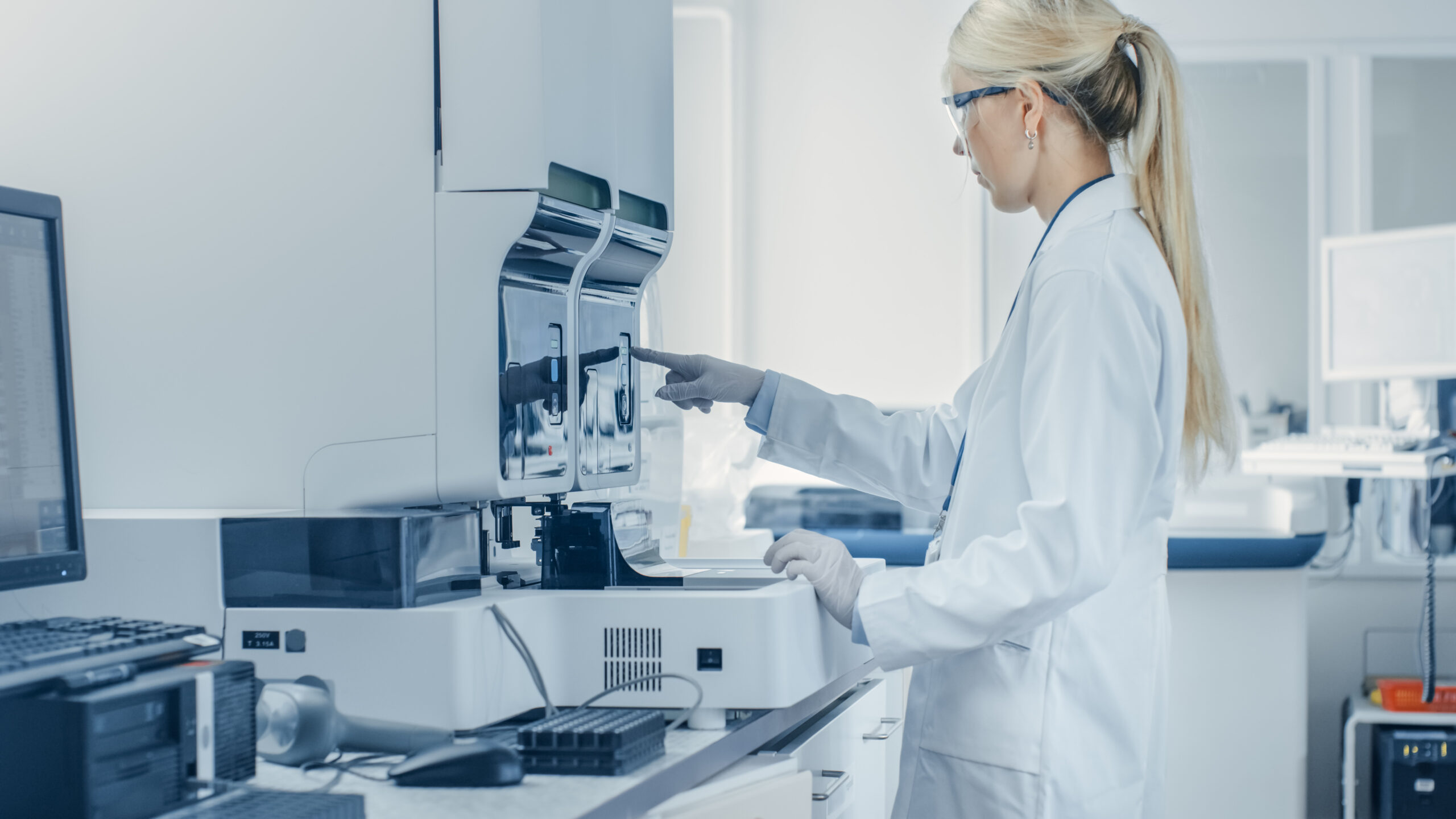
Phase 6
Full Production and Commercial Launch. At this point the product is in full manufacturing mode. Distribution and shipping methods should be in place, and any approvals in place.
Phase 6 activities:
- Full-scale manufacturing and assembly of the product.
- Product stability studies completed (and ongoing) to validate shelf-life claims.
- Finalize QA documentation.
- Implement marketing & distribution plans.
- Collect and review any customer feedback after product release.